A common path to achieving compliance to the European Union’s (EU’s) EMC Directive 2004/108/EC (which I shall call the EMCD here) takes many manufacturers down the route of utilizing a third-party EMC test laboratory to obtain EMC test reports for their products. This process was detailed in the article “Heading for the EU? Get Your Compliance Passport Ready1” appearing in the May 2013 issue of In Compliance.
However, it is important to understand that the EMCD contains no legal requirements for performing any EMC laboratory tests. Conformity Certificate Medical Equipment
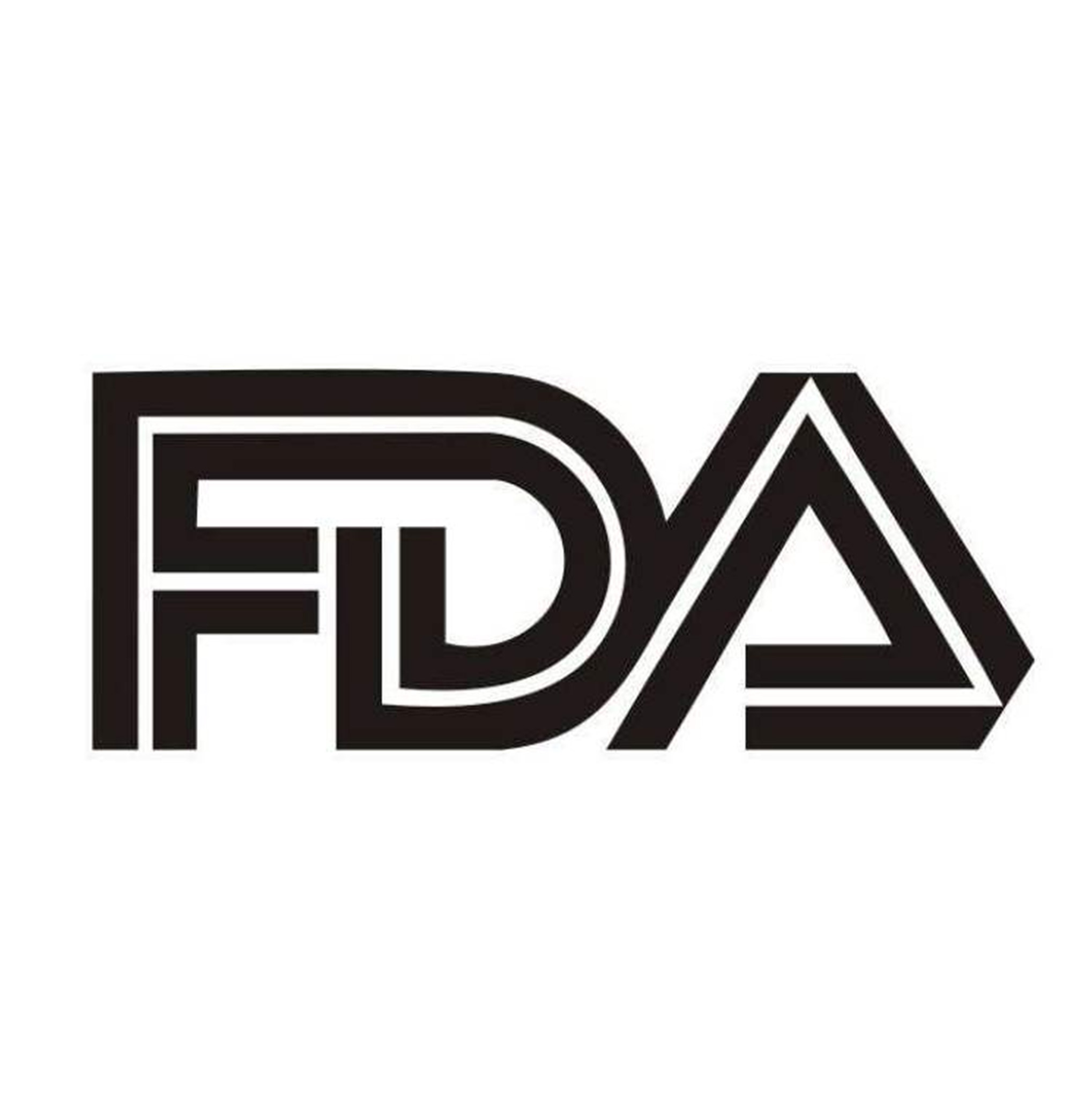
This was also true of the original EMCD, 89/336/EEC, and will also be true for compliance with the future EMCD, 2014-30-EC, which replaces the current EMCD on 20 April 2016 (more on this below).
Manufacturers are required to affix the CE marking to their products, and to do that they must first have created and signed an EU EMC Declaration of Conformity (DoC) which is based on the evidence of EMCD compliance contained within a Technical Documentation File (TDF).
As I will show later, there are two routes to declaring EMC compliance (sometimes called conformity to the EMCD), and it is the manufacturer’s choice whether his DoC relies entirely on all relevant harmonized standards (the Standards Route), or uses just a few or none of the relevant harmonized standards (the EMC Assessment Route).
Even when following the Standards Route, the DoC is effectively a legal statement by a manufacturer that: “if my product was tested to these harmonized standards, it would probably pass.”
How a manufacturer obtains sufficient confidence to make this legal declaration is entirely up to that manufacturer, and should be documented (amongst other things) in the TDF.
Compliance with the EMCD certainly does not require any test reports from third-party EMC test labs. This is what makes it possible for many manufacturers of electronic products around the world to save time and money by testing in their own EMC labs.
This also makes it possible for individual entrepreneurs, who might be working out of their garages (like Mr Hewlett and Mr Packard did when they first started)3 to sell their products in the EU without the high costs associated with EMC testing to standards.
In fact, the same is true for most of the so-called CE Marking Directives – third-party testing is only a legal requirement in a very few EU Directives, and only then when dealing with especially dangerous products, e.g. certain kinds of medical equipment; especially dangerous machinery such as chainsaws, bandsaws, etc.
I have often heard the EU’s single market described in the USA as Fortress Europe – when the exact opposite has always been true: the EU’s single market does not present any significant barriers of cost or delay to any equipment from anyone, anywhere.
OK, that’s enough background. Let’s get into the details!
To see how it is that manufacturers can comply with the EMCD without third -party testing, even without any testing at all, we need to understand how the EMCD works.
When we understand this, we will also understand that even passing third -party laboratory tests to all relevant EU harmonized EMC standards might not, on its own, ensure compliance with the EMCD.
The EMCD2 applies to both apparatus and fixed installations, with special legal meanings for both of these otherwise commonplace terms. Figure 1 shows that apparatus is treated very differently from fixed installations.
Figure 1: Applying the EMC Directive
Apparatus is any electrical/electronic item that could cause or suffer EMI, and which is “made available for an end-user in the EU” for the first time (see later). It is important to understand that the EMCD applies to every individual item (e.g. individual serial numbers) – Chapter 2.2 in [4] and Chapters 1.2 and 3.2.2 in [5] provide much more detail on this.
The EMCD also has a special category of apparatus “…intended for incorporation into a given fixed installation, and not otherwise commercially available” (which most of us would call custom, bespoke, or one-off equipment) which can avoid having to be CE marked for EMC, although it then has to comply with other EMC activities.
EMC Benign equipment is excluded from the EMCD’s scope, and the official guide [5] contains a list of what is currently considered to be EMC Benign. As a general rule, EMC Benign equipment never contains any operational semiconductors (rectifiers, transistors, ICs, etc.) or thermionic valves, or makes sparks.
Equipment that is only made available for the exclusive use of professional integrators in the construction of their own products, and which is not made available for end-users (even by distribution) is also excluded from the scope of the EMCD.
However, such equipment will almost certainly have to be CE marked for compliance with an EU safety directive, such as the Low Voltage Equipment Directive [6], Machinery Directive [7], etc. This is one reason why a manufacturer should never assume EMC compliance when purchasing a CE-marked third-party product for incorporation into another product, system or installation.
I have seen many large projects suffer greatly from major contractors making two big errors regarding EMC:
i. Mistakenly assuming that every item of equipment that carries a CE marking must perforce comply with the EMCD. This article describes three ways in which this assumption can be wrong, all of which are shown in Figure 1:
ii. Mistakenly assuming that an EMC compliant final system merely needs EMC compliance for its constituent parts, often called the CE + CE = CE approach (see later).
Also exempt from the EMCD is radio amateur equipment that is not commercially available; aeronautical equipment covered by Regulation 1592/2002, and equipment covered by the R&TTE Directive (1999/5/EC).
The new Radio Equipment Directive 2014/53/EU will replace the R&TTE Directive from June 12, 2016, at which time some of the equipment that used to be covered by R&TTE will instead come under the EMCD [2] and the LVD [6].
Equipment that has EMC aspects addressed in specific product Directives (e.g. medical devices, automotive, etc.) is only exempt from the EMCD to the extent covered by those other Directives. Unfortunately, this is widely misunderstood to mean they are totally exempt from the EMCD.
Apparatus that must comply with the EMCD when made available for an end-user in the EU may be advertised or exhibited before it is EMC compliant – as long as it is clearly marked as being non-compliant with the EMCD, and as not (yet) being available to end-users in the EU.
The EMCD requires all apparatus to:
Items i – v in the above list must be complete before the CE marking is applied (item vi).
All of the items i – vi must be complete before the apparatus is made available for the first time to an end-user in the EU (see 2.2 in [4]).
It is important to note that being made available to an end-user for the first time in the EU, does not only mean new products. Used or second-hand products that are brought into the EU are also made available for the first time in the EU, and so have to comply with the EMCD no matter how old or how large they are.
As already mentioned, the only exclusion to full compliance with the EMCD is for apparatus intended for incorporation into a given fixed installation, and not otherwise commercially available (see later).
The Protection Requirements (Clause 1 of Annex I in [2]) state the essential legal requirements for compliance with the EMCD, using simple terminology in the hope (probably a vain one) that this will make it difficult for lawyers to interpret them in ways other than what was intended:
“a shall be so designed and manufactured, having regard to the state of the art, as to ensure that:
(a) The electromagnetic disturbance generated does not exceed the level above which radio and telecommunication equipment or other equipment cannot operate as intended;
(b) It has a level of immunity to the electromagnetic disturbance to be expected in its intended use which allows it to operate without unacceptable degradation of its intended use.”
Who would ever want their products not to comply with these Protection Requirements? The costs of dealing with the resulting complaints (and the loss of possible future sales) would eat into the financial bottom line, making a manufacturer less profitable.
So even if there was no EMCD, the Protection Requirements above should still be applied to help reduce financial risks.
Conformity assessment is specified in Annex II of [2], and requires an EMC Assessment that results in a TDF that demonstrates how it is that a product can claim compliance with the Protection Requirements. The TDF should cover all operational modes and all intended use configurations, and (as described in [1]) the amount of verification work required can be reduced by identifying the worst case combinations of configuration and operational mode – i.e. the ones that would cause the highest emissions or are the most susceptible to interference. See 3.2.1 in [5] for more information.
As I said earlier, there are two routes to conformity with the EMCD:
Conformity Assessment by Using Harmonized Standards
When following this Standards Route, the product’s DoC must list all of the relevant harmonized EMC test standards that apply to the product, which can be found in the official listing website at [8].
This route to EMC conformity requires that all these harmonized standards are correctly applied – but what does correctly applied actually mean?
Clearly, one way is to have a third-party test lab perform all of the tests exactly as described in the relevant standards, with the EMC test reports forming the bulk of the TDF. If the test lab is accredited by a national accreditation body to perform a particular test, there is more confidence that the test will be done correctly. Unfortunately my experience (and that of many others) is that not all national accreditation bodies are equal.
Third-party testing has been very well described in [1], so I don’t need to go into it here.
Some manufacturers (and not only the larger ones) have their own full-compliance EMC test labs, and some of them even have some/all of their tests accredited. These labs are generally best used just as if they were third-party labs, as described in [1].
(Interestingly, in-house test labs located in the same building as the design teams can pay back their original investment much more quickly than the usual business case predicts – I have seen one such lab payback in four months!)
However, as stated early on in this article, using the services of a third-party accredited test lab to correctly apply a harmonized standard to test exactly to the standard is not the only option when following the Standards Route.
The correct application of a harmonized standard, actually means that a manufacturer has done enough homework to have sufficient confidence that if the product was fully tested in an EMC laboratory that was accredited to test to that standard – it would pass.
Let’s be perfectly clear on this: correct application does not mean that the product has actually been tested to that standard, only that – if it was tested at some future time – it would pass.
The EMCD leaves manufacturers totally free to decide on the amount and quality of EMC testing they do themselves, or have done for them, to have sufficient confidence to sign their DoC when using the Standards Route.
(It is important to understand that there are no absolute guarantees in the world of EMC – even with fully-accredited third-party testing, a product that passes in one test lab can fail when tested in another lab, even though nothing has changed in the product and the exact same cables are used with it. Some manufacturers take advantage of this by always using test labs that they find are more likely to give them a pass result!)
Here are four examples of when laboratory testing might not be required to correctly apply a harmonized radiated emissions standard such as EN 55022:
1. When the product emits a certain amount of RF power spread in a particular way over a particular frequency spectrum, and calculations/simulations show that if this emitted power was measured according to the relevant EMC test standard, it would be almost certain to pass (even when taking measurement uncertainty into account).
For examples of this approach, see [9] [10] and [11].
2. When the product is housed in a well-shielded and well-filtered enclosure that has been proven by shielding effectiveness testing and/or simulation to provide more than sufficient RF attenuation to ensure that if its emitted RF power was measured according to the relevant EMC test standard, it is certain to pass (even when taking measurement uncertainty into account).
Many manufacturers purchase well-shielded/filtered overall enclosures, then ruin them with modifications, completely wasting their high cost, see Chapter 5 of [12]. So an expert assessment is usually required to have sufficient confidence in the final assembly.
3. When a product fails in a test lab and a simple modification applied by hand makes it pass, and the same modification is applied on production units, there can be sufficient confidence that if a new production sample was retested, it would pass.
In this context, ‘the same modification’ means physically and dimensionally the same – for example an additional shield bond made with a screw-fixing is not the same for EMC as an additional bond made in a different place, or made in the same place with a braid strap or piece of green/yellow wire instead of a screw.
4. When a product has passed an equivalent or tougher radiated emissions test and has not been changed (either in its hardware, software, or components).
A typical example is a product that has passed MIL STD 461 radiated emissions tests which set lower emissions limits than the relevant harmonized test standard, see [13].
Chapter 3.2.2 of [5] provides very good guidance on the Standards Route, and states that where a product follows this route there is no legal requirement in the EMCD to perform the EMC Assessment process outlined below.
Unfortunately, even when full testing is done in a lab that is accredited for that test, and passed, it might not ensure compliance with the Protection Requirements in real-life operation, which is, of course, what really matters for compliance with the EMCD – and also (more importantly) for financial success.
This is because no harmonized test standards cover all of the EM disturbances that could occur in real life. Also, it is because the tests have been specifically developed to ensure repeatability in testing, which can often mean they are simply not representative of real-life EM disturbances.
Also – given the inevitably slow pace of international standardization – all published standards are behind the times. For example: none of the harmonized immunity standards cover the very close proximity of cellphones, e-book readers, Wi-Fi transmitters, RFID transmitters (including active RFID tags), etc., even though such proximity is now a normal “…electromagnetic disturbance to be expected in its intended use…”.
Immunity to the near-fields (see [14]) that can be created by portable RF transmitters in very close proximity is arguably now a necessity for legal compliance with the Protection Requirements, even though not tested by any harmonized standards.
“Big deal”, you might say, “but I don’t want to spend any more on legal compliance than I have to!” OK, but think for a minute about what I said earlier in the section on Protection Requirements – if products don’t comply with them they are less likely to be financially successful. If they have big problems with EMC in real life, they could even do irreparable damage to a manufacturer’s brand image and future profitability. Some companies have actually been bankrupted by real-life EMC problems.
The real reason we need to achieve EMC compliance, is to have products that work well enough in real life and don’t upset customers. Achieving this is important to help control financial risks, and so what if we have to produce a few pages of legal documentation for EU sales, when it merely covers EMC work we have already done?
For these reasons, when following the Standards Route, in addition to correctly applying all relevant harmonized standards, I always recommend performing a full EMC Assessment as below, then doing whatever else it takes to ensure conformity to the Protection Requirements. This can sometimes be as quick and easy as a check for emissions or immunity using a close-field probe [15].
Note: When following the Standards Route, the DoC should not state that the listed harmonized standards have been tested and/or passed (unless they have been, of course!). Generally, it is better for the DoC to say something like: “The following standards have been applied.”
Conformity Assessment by Not Using Harmonized Standards
This is the other route to EMC conformity permitted by the EMCD – the EMC Assessment Route.
When following the EMC Assessment Route, a manufacturer declares the EMC conformity of his apparatus directly to the EMCD’s Protection Requirements, using just some of the relevant harmonized standards, or just some parts of some harmonized standards, or even ignoring all harmonized standards completely.
The EMC Assessment Route must follow a specified technical methodology to ensure that the Protection Requirements are met.
According to 3.2.3 in [5], the EMC Assessment Route is usually more appropriate than the Standards Route in the following situations:
Of course, a manufacturer may choose to follow the EMC Assessment Route simply to save time and money – which is often the case for start-up companies who cannot afford the cost of laboratory testing.
This alternative conformity route is essentially the old Technical Construction File (TCF) route under the first EMC Directive (89/336/EEC) – but with the significant difference that now there is no legal requirement for any TDFs to be assessed by a third-party (see Notified Bodies, later).
Non-harmonized methods of demonstrating conformity with the Protection Requirements, that may be able to be used, either singly or in suitable combinations, as part of an EMC Assessment Route include (but are not limited to):
The EMC Assessment Route’s technical methodology includes (but is not limited to)—
a. Assessing the EM environment(s) normally expected at the user(s) location(s), taking into account (see [17]):
b. Create the EMC specifications for the product.
To help make life easier, these often use modified versions of harmonized standards, basic IEC test methods (see [1]), other EMC standards (automotive, military, aerospace, etc.), and/or guidance for systems and installations such as [12] [18] [19] or some of the many references they contain.
c. Verify and/or validate the product’s design against the EMC specifications.
Verification and validation techniques include – but are not limited to – EMC testing.
The 3rd Edition of the EMCD, 2014-30-EC, Applies From 20 April 2016
All of the technical compliance issues discussed in this article, and in [1], are unaffected by the third edition of the EMCD [20]. Its changes are more to do with adapting the existing EMCD to the EU’s New Legislative Framework (NLF, see Chapter 1.2 of [4]).
The changes wrought by the NLF are mostly concerned with extending legal compliance requirements to all economic operators through whose hands EMCD-compliant products pass, including: the manufacturer of the products (obviously), appointed agents, distributors, importers, etc.
CE + CE Does Not Equal CE
Constructing systems only from items that are CE-marked, and mistakenly assuming that this alone takes care of the EMC compliance of the overall system or installation, is often called the CE + CE = CE approach. Which simply doesn’t work!
This incorrect approach is very widely used by system integrators, installers, and major contractors. However, it is easy to show that, technically and/or legally, this approach should never be relied upon, and Chapter 1.2.2 in the official guide [5] contains a specific warning against using it. More detailed information on this is given in Chapter 1.5 of [12], Chapter 2.3.4 of [18] and Chapter 2.3.3 of [19].
Note that the CE + CE = CE approach is also incorrect technically and/or legally for most, if not all other EU Directives, including [6] and [7].
There’s a great deal more I could write on complying with the EMCD, but I’ve covered the main issue of how to comply without using laboratory testing, and wandered off into some related issues as well.
To find out more about related issues, here are some excellent sources of free information:
Keith Armstrong is a Principal Consultant with Cherry Clough Consultants Ltd, www.cherryclough.com, and can be reached at keith.armstrong@cherryclough.com.
Keith graduated from Imperial College, London, in 1972 with an Honours Degree in Electrical Engineering. He has been a member of the IEE/IET since 1977 and a member of the IEEE since 1997. Appointed as a Fellow of the IET and a Senior Member of the IEEE in 2010. After working as an electronic designer, project manager and design department manager, Keith started Cherry Clough Consultants in 1990 to help companies reduce financial risks and project timescales through the use of proven good EMC engineering practices.
Over the last 21 years, Keith has provided design consultancy and training courses to over 700 customers worldwide, presented many papers and published many articles and three books, all on good EMC engineering techniques, and on EMC for Functional Safety.
Keith’s field-proven approach applies good EMC engineering techniques at every level of design to achieve: savings in design/development costs and timescales; quicker time to market; improved functional specifications with lower overall-cost-of-manufacture; greater reliability and reduced warranty costs. (Plus easy and quick compliance with EMC regulations, of course!)
After working as an electronic designer, then project manager and design department manager, Keith started Cherry Clough Consultants in 1990 to help companies reduce financial risks and project timescales through the use of proven good EMC engineering practices. Over the last 20 years, Keith has presented many papers, demonstrations, and training courses on good EMC engineering techniques and on EMC for Functional Safety, worldwide, and also written very many articles on these topics. He chairs the IET’s Working Group on EMC for Functional Safety, and is the UK Government’s appointed expert to the IEC committees working on 61000-1-2 (EMC & Functional Safety), 60601-1-2 (EMC for Medical Devices), and 61000-6-7 (Generic standard on EMC & Functional Safety).
Your email address will not be published.
Save my name, email, and website in this browser for the next time I comment.
In Compliance is a leading source of news, information, education, and inspiration for electrical and electronics engineering professionals.
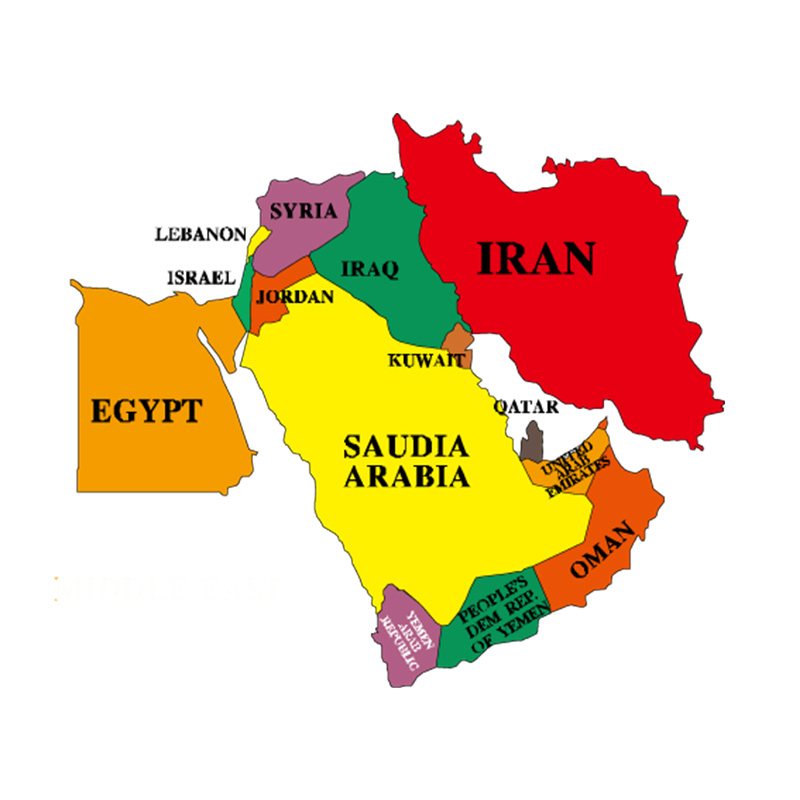
Ce Medical Device Aerospace Automotive Communications Consumer Electronics Education Energy & Power Industrial Information Technology Medical Military & Defense